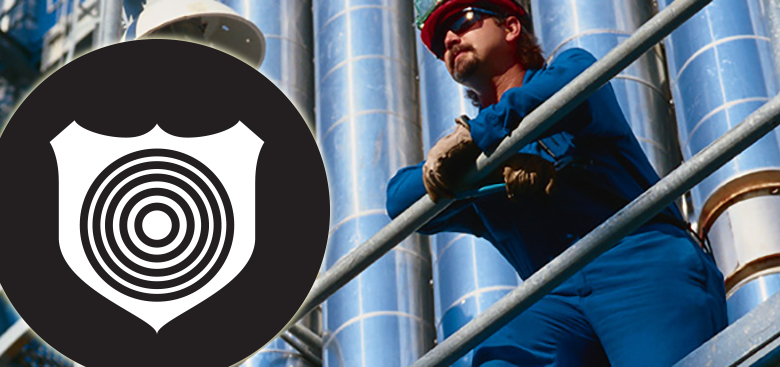
Protecting personnel, assets and the environment are the highest priorities for manufacturing and industrial plants the world over, from chemical and petrochemical facilities to water and wastewater treatment sites.
In a hazardous environment, reliable gas detection solutions can mean the difference between a fire or explosion spreading beyond all control. An early form of detection that minimises the risk of disastrous consequences and triggers a response could prove to be lifesaving.
For many people working in an industrial environment, dealing with hazardous and potentially deadly substances is all part of the day job. It is a given that you have to plan for, protect against and even brave hazards from potentially explosive atmospheres to chemical spills, which can readily burn or explode. Explosive atmospheres can be caused by flammable gases, mists or vapours or by combustible dusts. The problem with gases is that they often do not behave as we would expect, so having a robust gas detection system in place is vital.
In industries where a myriad of different fire hazards are present, minimising risk so that important day-to-day jobs can continue as normal should be a central part of a company’s safety solutions. Gas detection is the first step to ensure worker safety and can act as an early warning, but there are many key components to optimise these solutions, thus maximising the safety and protection afforded by reliable gas detection. To ensure optimal performance, the type of detection method has to be chosen carefully to match the type of gases present and prevent false alarms.
Explosion Protection & Plant Safety
In almost every individual application, flammable substances are used and gas detection systems must become reliable protection systems. Wherever there are hazardous situations due to the presence of combustible gases and vapours – for example, in processes involving the use of solvents or in the plastics processing industry – explosion protection measures must be in place as regulated by law, to ensure personnel and plant safety. These systems are designed to trigger an alarm in sufficient time to inform the operator and perform counter measures for the prevention of a potentially explosive scenario. The safety concept of a gas detection system always follows this protocol; detect dangerous gas, react and avert.
It is hard to believe, but even oxygen, the very elixir of life, can be a potentially dangerous fire hazard. It behaves very differently to air, compressed air, nitrogen and other inert gases and is very reactive. Even a small increase in oxygen levels in the air can provide the conditions for fire to spread much quicker and burn more fiercely. Depending on the application, different measuring principles for the detection of flammable gas and vapours can be used – for example, catalytic bead sensors, point or open-path infrared sensors and the system should be tailored to the individual needs of the operator. When combined with a central controller, it is possible to detect flammable vapours and gases such as hydrocarbons and hydrogen at an early stage, where concentrations are so low that a dangerous condition or risk of explosion can be reliably averted.
Identifying Risks
Before deciding on the appropriate measure of gas detection, which undoubtedly will be a bespoke solution for every organisation, it is important to get back to basics and identify the gas detection system that will support your workforce’s safety goals. Considering the following points is an important means by which to identify the risks and determine the most appropriate means of gas detection and can be applied to any situation:
- What potential worksite hazards exist?
- What alarm time is most appropriate given the hazards present?
- Does the project require portable or fixed gas detection?
- What environmental conditions must the system withstand?
- How do my employees work best and what type of system will allow for ease of use?
- Do we need to look at a single worksite or multiple locations?
- What training will be most effective for my employees?
Wherever toxic or flammable chemicals are being manufactured, processed, stored or shipped, there will always be a risk of an accident or substance release. Even the smallest release of substances can cause harm to people, damage the environment or even destroy property. Essentially, any gas is potentially dangerous, whether liquefied, compressed or in a normal state.
There are three categories of risk that must be detected reliably in order to protect human life, assets and the environment.
- Ex – risk of explosion by flammable gases.
- Ox – oxygen; risk of asphyxiation by oxygen displacement or risk of increase of flammability by oxygen enrichment.
- Tox – risk of poisoning by toxic gases.
Without auxiliary tools, people are often unable to recognise these dangers early enough to initiate appropriate counter measures. In a gas processing plant for example, where there are a myriad of hazards presenting themselves at any one time, managing risk and having in place substantial gas detection systems plays a major role in the mitigation or prevention of a major accident or incident.
It is the responsibility of any company operating in a hazardous area to carry out the appropriate risk assessment depending on the probability of the occurrence of toxic or explosive incidents. Certain areas present a higher risk probability, yet if such locations are not easily identifiable it is important to distribute gas detection sensors across the entire hazardous areaaccording to industry prescribed methods to help to manage the risk.
It follows that the necessary steps should be put in place and the most appropriate gas detection methods employed, to ensure workers are alerted to harmful gases if the situation arises and human lives, as well as industrial facilities, are protected.
Sniffing-out Gases
Our sensory organs are often unable to detect airborne hazards or cannot do so early enough. Toxic or flammable gases and vapours can build up reaching hazardous concentrations, or there may be insufficient oxygen in the air, which can result in a life-threatening situation. A detection system must respond reliably to a variety of gases, identify them and measure their concentration in the ambient air. Any such system needs to be meticulously planned and carefully considered before being implemented.
When it comes to gas-related accidents, most eventualities do not ‘just happen’. Each of these accidents is more often than not, a culmination of a series of individually minor events that combine and add up to cause a more serious problem. The detection of even the smallest gas leak for example, can avert a chain reaction that would otherwise take on a life of its own and even threaten lives. These leaks can arise when cold, liquefied and other pressurised gases are released into the ambient air and mix with it. Their concentration decreases and the gas dispersion depends more on the current temperature conditions and ambient air convection than on the density of pure gas.
Usually invisible to the naked eye, often odourless and impossible to hear, many substances are undetectable to the human senses – but leaks of these gases and vapours can pose a very dangerous threat to both people and places. Depending on their substance, quantity and location, gas leaks can cause everything from immediate ill health to plant shutdowns and potentially explosive situations.
Critical points where the release of gases could occur include all types of storage vessels, including valves and pipes, as well as in machinery and pumps. Dynamic loading as a result of temperature and pressure variations, corrosion and material fatigue are important factors that may lead to leakage from joints and seals and filling and tapping points also need special attention. There is also the issue of technical leakage to consider, whereby material is deliberately released through valves, diaphragms and overflows to prevent malfunction. The most notable incidents are those in which dangerous substances are released. In this form of release, gases form a cloud around the leakage point and the edge of the cloud becomes a turbulent boundary zone. A comprehensive mapping exercise will accurately identify
As well as differences in gas behaviour, there are also differences between gas detection in confined spaces and in the open air. The conditions for the formation of gas clouds in interior spaces are similar to those in the open air but gas clouds behave very differently in an enclosed space. In cases like these, the architecture, convective flows and ventilation determines the spread of the gas. Pools of heavy vapours are especially dangerous as they can form on the floors of enclosed spaces such as cellars and tanks.
The Role of Gas Detection Systems
Gas detection systems are fundamentally products of safety technology, used to protect workers and ensure plant safety. It is important not to misinterpret the role such a system. They are not simply a handful of detectors spread across an industrial plant; rather they should be considered a bespoke solution developed to meet individual protection objectives.
Gas detection systems can be portable gas measuring instruments or fixed installed gas detection systems. The safety of an area potentially being affected by dangerous gases and vapours to a high degree depends on the reliability of the gas detection system and the quality of the sensors being used. We often find that fixed installed systems are in operation continuously, 24 hours a day, year after year, to ensure that they are alerted under any instance of a random gas release, as well as operating under extreme environmental conditions.
Past events show that fires can spread rapidly causing devastating consequences to industrial plants and surrounding areas.
So, How Do We Protect Against Gases Behaving Unpredictably?
Many toxic and flammable gases are very reactive and under suitable conditions they can change by chemical reactions. Modern gas detection systems utilise a multitude of techniques in their operations; from electrochemical sensors and catalytic bead sensors to infrared technology in point sensors and open path sensors, as well as flame detectors, ultrasonic sensors and gas cameras. Just as gases can display unusual characteristics, the real innovation in gas detection technology is in the very precise matching of the measuring system to localised circumstances and particular requirements.
With ever-improving sensors, modern detection technology for flammable and hazardous gases enables us to design highly reliable gas detection systems. The foundation for planning any system is well-considered matching of the components, based on a range of different technologies, to specific local conditions.
Holistic Solutions
Safety needs cannot be met by ‘off-the-peg’ solutions and it is important to undertake a detailed analysis of the current situation to ensure that all individual needs in gas detection are met, providing an holistic solution.
Significantly, no one detection system can work in isolation, hence the role of bespoke solutions and the importance of tailoring a company’s safety systems to its individual needs. Gas detection systems can be supported effectively by explosion-proof and reliable flame detection systems. It is important to have in place a full and tailored solution according to your needs and driven by the application including substance, surrounding environment and processes, fire type (hydrocarbon or non-hydrocarbon) and size.
To ensure that a gas detection system is able to react quickly and precisely, its components must be carefully matched to the particular circumstances such as the physical and chemical properties of the materials, assumption of the most likely leakage points, as well as the location’s constructional, geographical and meteorological conditions.
The prediction of gas dispersion and most likely behaviour, based on particular circumstances, forms the basis for a gas detection system, whether stationary or mobile. Fundamentally, in order to ensure a system’s reliability, it must be correctly installed, calibrated, operated and maintained. It follows that within every tailored gas detection system should come a bespoke training and servicing plan, an area which MicroWatt believes is absolutely imperative in ensuring the safety of human lives.
Making sure there is a robust system in place could mean the difference between life and serious injury or even death.
Learn more about MicroWatt’s Explosion Proof Gas Detection
Ref: Mdm Ltd Publishing
Article Link: http://ifpmag.mdmpublishing.com