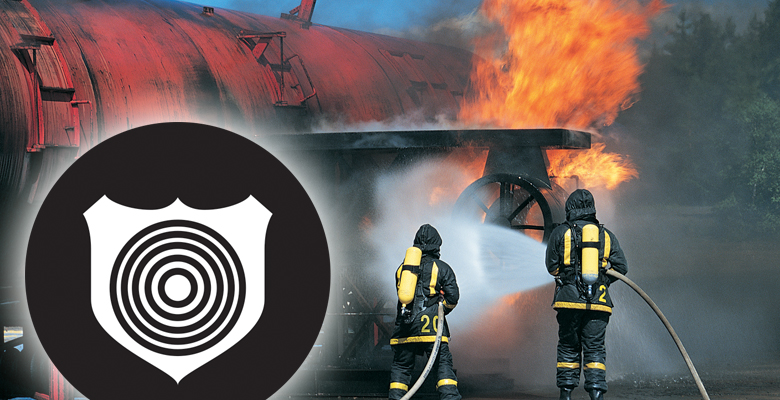
Curious as to why multi-spectrum IR flame detectors were developed and rapidly adopted as the optimal choice, replacing UV/IR flame detection in oil and gas facilities? Read on friends!
Those with deep history working with flame detection in the oil & gas industry can tell you that combining Ultraviolet [UV] and Infrared [IR] sensing technologies was the first significant advancement by product engineers to improve the performance of traditional UV flame detectors, which were extremely problematic with respect to nuisance alarms, unwanted shutdowns and costly maintenance procedures. Many years later, an even more significant leap forward in flame detection technology eliminated the UV sensor, the culprit in many false alarms and maintenance requirements, and added 2 IR sensors [triple infrared / 3IR being the most common design] with optical filters and advanced micro-processor signal analysis, which took the performance to another level altogether.
Why was this done? What was the issue?
The short answer is: petroleum!
Unlike IR energy emitted by flame, the UV radiation emitted is readily absorbed and attenuated by most hydrocarbon substances existing between the sensing element and the flame – whether airborne like vapour, oil mist, and smoke and certain other chemicals or deposited on surfaces in the optical path of the detector such as the inside of lenses, outside of lenses or on reflectors utilized for self-checking.
Triple IR and multi-spectrum IR flame detectors are virtually unaffected by these hydrocarbon attenuating substances which are commonly present in oil and gas facilities. Furthermore, these multi-spectrum detectors are able to detect hydrocarbon-based flame at up to 4 times the distance with improved false alarm rejection AND they detect flame of non-hydrocarbon fuels such as hydrogen, ammonia and sulphur.
It is stated in the product literature published by premium flame detection manufacturers* that UV/IR detectors will fail to detect flame without simultaneous detection of both UV and IR radiant energy in prescribed ratios and magnitude. This limitation is not present in triple IR detectors.
So regardless of any electronic reliability ratings such as SIL, performance certifications, sensitivity settings or field-of-view dimensions, the critical function of detecting flame using a UV/IR device is severely compromised when the emitted UV energy from a flame has been obstructed by airborne hydrocarbons or deposits of hydrocarbon material on critical optical surfaces. You may be thinking the optical self-test feature would notify operators of this unsafe condition, and it might. Reflectors are often very small and difficult to access at the periphery of a lens and it is not unusual for them to become fouled and they can be very difficult to clean in the field. In some detector models servicing of reflectors requires the removal of the entire detector from service while it is returned to the factory for service. Optical integrity tests provide operators with a notification of a detector that is in fault, but the detector must be serviced immediately to restore safe function and for prescribed performance levels to resume. Until full functionality is restored, your critical last line of defence in the event of a fire is failing to provide the intended risk reduction.
External reflectors and test light sources are utilized by the majority of optical flame detectors in order to perform automatic optical self testing, however there are a few innovative designs which have eliminated external reflectors for the self-test function and thus provided significant performance, reliability and maintenance advantages for users.
In addition, operators should consider that substantial reduction of flame detection capability and reduced detection range occurs long before optical fault detection schemes are activated. Optical self-test faults are typically triggered after flame detection sensitivity has been reduced by ~50%. By application of the inverse square law for emitted radiation it follows that a fire must be 4 times the baseline detectable size (published sensitivity) to be detected when approaching a 50% reduction of sensitivity. Field-of-view and speed of response may also be adversely affected by sensitivity reductions before an optical fault is detected.
If and when optical faults due to hydrocarbon deposits are detected, immediate attention is required to clear the fault condition and restore normal operation. This usually involves by-passing the detector alarm outputs and deployment of time-consuming and resource-intensive, 2-man, manual maintenance activities involving high risk operations at heights requiring ladders, scaffolding, or mechanical lifts to access and clean flame detector lenses and reflectors.
It is understandable that choosing a flame detector that has eliminated the external reflector contributes to significant maintenance cost savings.
Lifecycle safety maintenance costs rapidly consume the small cost savings related to selection of choosing UV/IR versus Multi-spectrum IR or Triple IR detectors.
Triple infrared designs also reduce false alarms known to occur in UV/IR detectors when either of the UV or IR bands are affected by external, non-flame radiant energy sources (false stimuli). If UV energy from non-flame sources are present in the environment as a result of faulty metal vapour lighting, it satisfies the UV sensor. The detector then behaves like a single band IR detector which can be more easily triggered into full alarm by normal hot surfaces in the facility (blackbody infrared radiators). Conversely, if strong IR sources such as hot process surfaces satisfy the IR band then the detector tends to function like a single band UV detector and is prone to false alarms due to faulty metal vapour lighting, arc welding at long distances, electrical arcs and lightning.
Advanced Triple Infrared flame detectors, particularly designs utilizing Wide-band IR, techniques eliminate these issues and are field-proven to deliver the highest immunity to known false alarms sources within heavy and light industrial environments. The primary difference between the first-generation 3IR and Wide-band 3IR principles of operation is that product engineers originally only had the ability to apply optical filters to IR sensors in an attempt to discriminate the strong radiation produced by common false alarm sources in industrial applications. These sources can bombard a sensor with stimuli, which filtered sensors cannot interpret – in certain conditions it will produce a fault, or even worse an alarm. The more advanced Wide-band IR design does not rely on optical filters: modern microprocessors and sensitive photoconductor sensors analyze the AC and DC characteristics of the entire flame emission spectrum, from the visible band through to the end of the infrared band. This design accurately identifies ALL fire characteristics within the signature, and the false alarm characteristics – delivering the highest immunity available.
Why were multi-band IR detectors developed and rapidly adopted as the best choice in oil and gas facilities?
- UV band is eliminated and with it many weaknesses as described above
- 3 to 4 times greater sensitivity yielding greater detection range
- Highest available false alarm immunity
- Lower overall cost of ownership through significantly reduced maintenance
Characteristics of next generation multi-spectrum flame detectors:
Multiple sensors in the infrared band are supplemented by a sensor in the visible band to further enhance false alarm rejection
Wide-band Photoconductor sensors engineered to analyze both AC and DC flame characteristics, identifying flame AND false alarm sources – going beyond the first-generation 3IR approach attempting to filter out powerful false alarm radiation sources
Field adjustable sensitivity allows easy adjustment for specific applications
Elimination of external reflectors for optical fault monitor greatly reduces maintenance
Economical and easily field replaced electronics module
Flame data logging with time and date stamping
Author: Ken Coffey
Ref: MicroWatt Controls
* Eg1. The simultaneous detection of radiant energy in both the UV and IR sensors then triggers the alarm.
* Eg2. Combines both IR and UV detectors in a single housing. Both detectors are required to detect simultaneous radiation before generating an alarm.