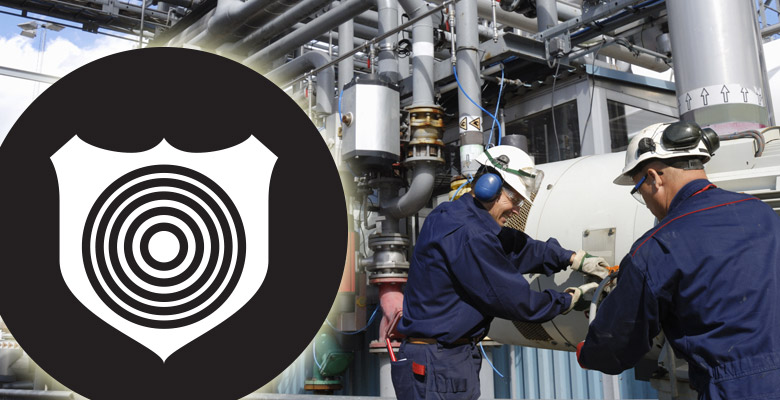
Protection Methods, Containment, Segregation, and Prevention
This article from Robert Schosker in association with ISA answers the question, “Why worry about hazardous locations?” The area classifications for North America and the European (the International Electrotechnical Commission [IEC] standard) approaches are described and contrasted, including protection methods, containment, segregation, and prevention.
What is intrinsic safety?
Intrinsic safety (IS) has been around a long time. It is the concept of limiting ignition-capable energy to below that of the hazardous material a process may be working with. IS, as most people call it, was born out of the ashes of a horrible mining accident in the U.K. in 1913. The explosion was caused by a low-voltage signaling system that was used to advise the surface crew that coal cars were ready to be brought to the surface. The ensuing research revealed that the most important factor in determining the safety of an electrical circuit is the energy stored in the circuit. The concept of intrinsic safety was born.
So why do we worry about hazardous locations? Many explosions are the result of limited knowledge by employees, which can be directly related to inadequate training, lack of documentation, and questionable safety measures. These disastrous results may have been prevented with proper training, new instrumentation, inspection, maintenance, or revised safety procedures. Of course, even if the plant takes these steps, an explosion could still happen; however, every effort to reduce “residual risk” is a benefit. Residual risk is the risk left over after all other forms or mechanical means of risk reductions have been taken.
A hazardous area is an area containing (or likely to contain) an ignitable concentration of flammable gas, vapor, or dust, where an electrical spark of sufficient power will cause an explosion. However, an explosion can only occur when an oxidizer, the hazardous substance (gas, vapor, or dust), and energy (thermal or electrical) are present at the same time. These three groups comprise what is known as the hazardous location ignition triangle.
/RS/w640.jpg?&ssl=1)
If any one of these groups is removed, an explosion cannot happen. As we will discuss throughout this article, intrinsic safety is a method of protection that removes one of these groups from the ignition triangle.
The article will first answer some basic questions about hazardous locations. We already know why we worry, but what are we worrying about? What is a hazardous location? What or who defines a hazardous location? What is the difference between zones and divisions? These are all very good questions, and ones that are often asked. We already know that a hazardous location is an area that contains or is likely to contain an ignitable concentration of flammable gas, vapor, or dust. Once we have determined that a hazardous area exists, then we classify that area using either zones or divisions. Although the physical principles of explosion protection are the same worldwide and are not differentiated, the procedures determined by national legislation in the approximately 100-year history of explosion protection have resulted in various solutions. Each solution has a unique perspective on how to classify a hazardous area.

Divisions, mainly a North American-approved method of classifying an area, use four categories: class, division, group, and temperature. They are commonly seen like this:

The categorization of these areas is carried out in North America in accordance with the National Electrical Code NFPA 70, article 500. Class I, II, or III represent the form of the hazardous material you must deal with.

Division is a categorization by the probability that these materials will be present in a potentially hazardous quantity (Division 1 and Division 2). The division is commonly the perimeter or designated area of the hazardous material.

Furthermore, classes of hazardous areas are divided into subgroups depending on the type of flammable gas or vapor present.
Finally, apparatus installed directly in a hazardous area must be classified for the maximum surface temperature that the device will produce under normal operation or in the event of a fault. The maximum surface temperature must be below the minimum ignition temperature of the gas present.

The graphical representation below illustrates the concept of division-based areas.

In Europe, the zone method of area classification is used. The European zone practice is described in IEC/EN 60079-10. In accordance with this standard, any area where there is a probability that flammable gas or dispersed dust may exist must be classified into one of the following areas:

The European zones then require that the apparatus be subdivided into two groups, according to IEC/EN 60079-0. These two groups in general terms indicate whether the apparatus is located above or below ground.

And as with divisions and gas groups, there are subgroups of Group I and II within the zones. Each is associated with a certain number of gases having an ignition energy in the value reported and is represented by the gas referenced in the table below. Included in this comparison are the Class I and II division-based classifications.

A temperature code is also required just like divisions; however, the zone method is simplified. With both divisions and zones, the maximum surface temperature must be below the minimum ignition temperature of the gas present.

The graphical representation illustrates the concept of zone-based areas.

The article has explained hazardous areas and how those areas are classified, but what methods of protection exist for your hazardous areas? As previously mentioned, to reduce the risk of explosion, you must eliminate one or more of the components of the ignition triangle. There are three basic methods of protection: explosion containment, segregation, and prevention.
- Explosion containment: the only method that allows the explosion to occur, but confines it to a well-defined area, thus avoiding the propagation to the surrounding atmosphere. Flameproof and explosion-proof enclosures are based on this method.
- Segregation: a method that attempts to physically separate or isolate the electrical parts or hot surfaces from the explosive mixture. This method includes various techniques, such as pressurization and encapsulation.
- Prevention: a method that limits the energy, both electrical and thermal, to safe levels under both normal operation and fault conditions. Intrinsic safety is the most representative technique of this method.
The protection methods, based on the containment and segregation concepts, are methods that contain the explosion in order to prevent the energy source-electrical or thermal-from coming in contact with the potentially explosive mixture. In both cases, the use of appropriate enclosures and specific wiring and installation systems is required. The intrinsic safety method prevents the ignition of the explosive atmosphere, while simplifying the installation and use of the required apparatus that is connected to the electrical circuits directly located in a hazardous location.
The choice of a specific protection method depends on the degree of safety needed for the type of hazardous area. The idea is to determine the best protection method based on the lowest probable degree of the simultaneous presence of an adequate energy source and a dangerous concentration level of an air/gas mixture. Of course, other important factors to consider include the size of the apparatus to be protected, the flexibility of the system, the possibility of needing to perform maintenance, and the installation cost. Respective of these factors, intrinsic safety has many advantages.
So what is intrinsic safety? Intrinsic safety is based on the principle of limiting energy to a level below that required to ignite the hazardous gas or dust. The energy limitation also pertains to thermal energy as well. Therefore, in normal operation or in the event of a fault, no sparks or thermal effects may occur that could lead to the ignition of a potentially explosive atmosphere.

It is one thing to understand intrinsic safety as a concept, but it has to be applied correctly to work. As shown in the illustration, there are three components to an intrinsically safe circuit:
The field device-intrinsically safe equipment located in the hazardous location
Intrinsically safe barrier or associated apparatus located in nonhazardous location
Interconnecting wire between the two apparatus
The example here is simple, because the fault combinations are few, and the knowledge of the apparatus safety parameters and cable characteristics are sufficient to verify the safety of the system. A more complex system (combinations of barriers or using multiple cables) requires a more detailed analysis because there are many fault combinations to verify, and they are not always evident.

As mentioned above, more complex analysis may be required with intrinsic safety, but with this in mind, intrinsic safety has several advantages over the other methods of protection. They include allowing trained personnel to connect and disconnect circuits under live operation. They are guaranteed to be safe during short circuits or lead breakage. Intrinsic safety is the only ignition protection class that allows connectors to be opened and intrinsically safe apparatus to be removed and replaced by an equivalent device in a hazardous area. Intrinsic safety is also the only method that allows general-purpose wiring methods to be used in the hazardous area. These simple advantages also generate cost savings through installation and maintenance, because this method allows live maintenance with no need for plant shutdown. Intrinsic safety is also more reliable due to the use of infallible and derated components as prescribed by the standards.
Intrinsic safety was born from the ashes of a horrific accident to become the most widely accepted method of protection. Not only does it limit voltage and current, but it provides a 50 percent safety margin even during fault conditions; no other method of protection can claim that. In the end, it is the end users who must determine the area of classification, the required process equipment, and the method of protection they want to use. If they decide to use intrinsic safety, I think they will find that it provides the best mix of an affordable system and the safety required.
Ref: ISA The International Society of Automation
Original Article By: Robert Schosker
Article Link: https://www.isa.org