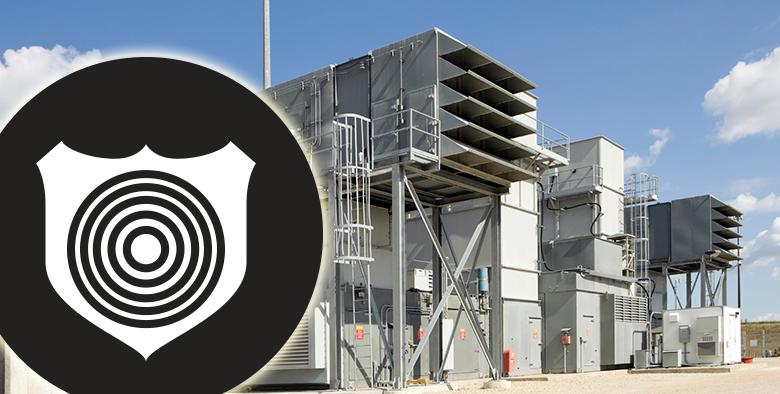
Unprotected facility ventilation systems can transport combustible and toxic gases from a source area to other parts of the building, bringing the dangerous substances into non-hazardous areas.
HVAC gas detectors protect control rooms, living quarters, electrical switch rooms, and equipment rooms by effectively reducing the risks from releases through early detection, quickly initiating a supervisory signal to an attending system, and triggering the appropriate automatic protective response.
Air handling systems are used throughout industry to provide comfort and health in manned areas. From systems that deliver fresh air in confined spaces to HVAC systems in living quarters, exhaust / ventilation systems form part of the essential safety services of chemical process and petroleum facilities. Nevertheless, if unprotected, facility ventilation systems can transport combustible and toxic gases from a source area to other parts of the building, bringing the dangerous substances into non-hazardous areas, like control rooms, living quarters, electrical switch rooms, and equipment rooms.
Because of the potential for the inadvertent transport of dangerous substances, government agencies, industry groups and many leading companies have established procedures for exhaust/ventilation system safety. One important element in the protection of these systems is gas detection. Gas detectors reduce the risks from releases through early detection, indicating a supervisory signal to a constantly attended location and initiating an appropriate automatic protective response. Activation of a sensor, for example, can cause an alarm signal and lead to HVAC shutdown and activation of damper controls to prevent the ingress of toxic gas clouds into work spaces.
Three key challenges regulate the design of gas detectors for duct applications: Air velocity, dilution, and stratification. Since air flows turbulently through ducts at 2,000 – 6,000 ft/min (23 – 68 mph), sensors must be designed to withstand high ventilation rates. Electrochemical sensors, which rely on the generation of current in an electrolytic solution to measure gas concentration, must be well sealed to prevent evaporation, particularly when exposed to dry air. Other sensors like catalytic and solid state devices must be able to control optimum reaction temperatures in the presence of strong air currents or have protective covers (splash guards, screens, or sinters) to prevent air from impinging directly on sensor elements.
A second challenge for gas sensing in HVAC systems is dilution. As air enters the duct network, it typically mixes with circulated air, which dilutes gas concentration several times. As a result, gas sensors tailored for duct applications must be highly sensitive. Low detection limits enable operators to set warning and alarm set points at a few parts per million, as low concentrations of detected gas may be indicative of much higher concentrations in the air stream.
Last, stratification presents a severe risk for gas detection. Since duct networks contain bends, expansions, contractions, and other features, uniform air flow in the cross section area is hardly ever the norm. Sudden contractions and expansions can create eddies where gases can accumulate, leading to the improper sampling of air. Gas stratification appears to have been at the source of an incident on the Brae Alpha platform in the North Sea and the subject of an investigation into the placement of flammable gas detection systems in offshore installations. To prevent the risk of failures to detect gas as a result of uneven mixing, detection systems are designed with extended sampling lengths or distributed across the duct width to ensure optimal area coverage.
The following is a list of strategies provided by the UK HSE Research report ref. RR602 (2007). This study was done with the use of CFD modeling to provide a basis for advice to inspectors and the industry on the effectiveness of flammable gas detection strategies for offshore HVAC ducts, but the strategies are applicable to onshore as well.
(1) Detector alarm levels should be set as low as reasonably practical: 10% LEL or less.
(2) Point catalytic, point infra-red, extended path point infra-red, cross-duct beam infra-red and aspirated point detector systems all have the potential to be effective in detecting non-uniform distributions of flammable gas in and around HVAC ducts provided that their sensitivity is sufficiently high (low detection limit) and that due regard is given to the possibility that gas will be distributed non-uniformly.
(3) Extended path point infra-red detector systems currently appear to offer the greatest sensitivity, but multiple detectors should be used and sited so as to anticipate non-uniform mixing.
(4) Cross-duct beam infra-red, extended path or aspirated point detector systems should be based on two approximately orthogonal beams or lines of aspirated point probes.
(5) No significant benefit can be expected to be gained from siting detectors inside an HVAC duct compared to locating them immediately outside the HVAC inlet.
(6) In the absence of purpose-designed mixing elements or a series of bends upstream from gas detectors no significant benefit is to be gained from siting detectors a significant distance downstream from an HVAC inlet.
(7) Mixing elements have the potential to reduce any non-uniformity in the distribution of gas in a duct but their effectiveness should be proven by physical tests.
With the growing acceptance of ISA TR84.00.07, a large number of facilities have chosen to increase the safety availability level (SA) of FGS functions by increasing redundancy or decreasing sensors’ functional test intervals. For this reason, plant safety personnel have dedicated greater resources to establishing methods that are fast and convenient, employing, for example, set-ups that allow easy access to the instruments or permit remote testing and calibration.
Exhaust/ventilation systems are often exposed to the ingress of smoke, combustible and toxic gases from hazardous areas. To reduce their vulnerability, these systems are often equipped with gas sensors, which are installed in a manner that anticipates the adverse effects of ventilation rate, dilution and stratification in order to detect gas accumulations in the low parts per million.
If mounting inside the duct-work is required, sensors can be installed downstream from the filters as air comes in from the outside and downstream of the air return. Sensors should be mounted along the duct cross section in order to ensure optimal area coverage and static mixers are introduced to prevent gas stratification. Where mixing elements cannot be installed, sensors should be located immediately outside the HVAC duct as there is no significant sensing benefit from being inside the duct (as stated in point 5 above).
Get more information on all our Industrial and Commercial Honeywell Gas Detection solutions.
Receive this Application Whitepaper – submit the form below
Ref: Greg Pajak – P.Tech (Eng.), MicroWatt ISA84 SIS Expert authored summary from: Walsh P, Johnson A, Ivings M (2005) Effectiveness of gas detection in HVAC ducts: Scoping study. Health and Safety Laboratory Report FM/04/11.
Article Link: https://www.linkedin.com/pulse/hvac-gas-detection-strategies-greg?trk=prof-post