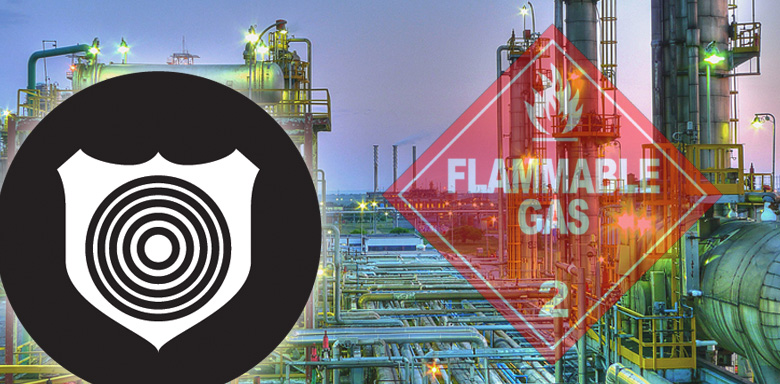
Introduction
Few gases match the broad use of ethylene in modern society. Ethylene is a starting material for the industrial synthesis of linear polymers, aldehydes, and a whole host of other major chemical products. Plastics, plasticizers, surfactants, food additives, and fibers are products of this major building block. At the end of 2006, global ethylene capacity was 121 million metric tons (28 million metric tons in the US alone) (1), making ethylene the most produced organic compound in the world.
Ethylene is highly reactive and explosive over a wide range of concentrations. Ethylene poses a fire risk over a larger span of concentrations than benzene and several short chain alkanes.
In addition, ethylene has among the lowest minimum ignition energies of industrial gases, a burning velocity that is approximately 35 to 60% greater than that of methane, and a high flame temperature. Such combination of physical properties contributes to making ethylene a significant workplace hazard. In the UK, for example, ethylene is classified as a dangerous fluid as defined in schedule 2 of the Pipeline Safety Regulations 1996 (PSR) (2).
Because of the hazards associated with ethylene leaks, safety equipment manufacturers have developed detectors that combine fast response, reliability, accuracy, and selectivity. Market trends toward increasing plant utilization have also prompted manufacturers to develop detection devices of comparably small size and low overall cost.
Several detection techniques are available to monitor ethylene; catalytic and infrared (IR) detection being the most reliable and proven techniques. Here we compare various sensor principles and evaluate their fit, given their states of development, to ethylene handling.
Detection technologies
Catalytic Gas Detection – A common technique for establishing the presence of ethylene is catalytic gas detection. Catalytic detectors employ catalytic combustion to measure combustible gases in air at fine concentrations. As combustible gas oxidizes in the presence of a catalyst, it produces heat and the sensor converts the temperature rise to a change in electrical resistance, which is linearly proportional to gas concentration. A standard Wheatstone bridge circuit transforms the raw temperature change into a sensor signal.
The simplicity of catalytic detector design belies several strengths that have made them a mainstay of fire and gas safety applications for over 50 years. Catalytic detectors are robust, economical, reliable, and self-compensating to changes in the environment like humidity, pressure, and temperature. They are also easy to install, calibrate, and use. Once in place, the detectors can operate for years with minimum maintenance, requiring only periodic gas calibrations to verify operation. Because the catalytic combustion reaction is non-selective, catalytic detectors can be used for monitoring several target gases across a wide range of applications. Catalytic sensors are suitable to detect ethylene in concentrations well below the lower explosive limit.
IR Gas Detection – IR detection depends on the ability of certain molecules to absorb light at wavelengths that are characteristic of molecular structure. The absorption characteristics are defined by molecular vibrational energies associated with stretching, bending, or rotations. In general, functional groups absorb radiation in characteristic wavelength bands. Ethylene, for example, exhibits distinctive spectral features in the 3.3 m region.
Combustible IR instruments employ a dual wavelength technique. In order to prevent distortions produced in the background due to source aging, contamination of the optical surface, or response to other gases, absorption at a particular band is monitored with respect to a reference measurement. Reference wavelength bands are chosen in a region of the IR spectrum where there is minimal absorbance of the gas of interest. Hence, using the differential absorption technique, both active and reference channels are equally attenuated when there are contaminants present in the IR beam.
The advantages of infrared combustible gas detection are well known. Infrared detectors can operate in oxygen deficient or enriched areas, are resistant to corrosion, and are fail safe. Failures like beam block or defective light sources are revealed, enabling operators to restore the device to full operation. Additionally, IR detectors require no routine calibration. Maintenance consequently involves occasional cleaning of dust screens and external optical surfaces and removal of any debris that may impair access of the target gas to the sampling chamber.
Infrared units configured for ethylene are also non-selective, hydrocarbon detectors that show varied response to other hydrocarbons. Exposed to 10% LEL methane, an ethylene point detector will measure about 65% LEL ethylene. Ethane, propane, and other gases with strong absorption in the near IR yield high % LEL outputs at low concentrations on ethylene infrared units.
Combustible IR detectors can be both point and open path. IR point type devices are used to detect ethylene in various concentration ranges, typically arranged in a three-dimensional array or in-duct mounted for HVAC (heating ventilation air conditioning) systems. In contrast, an open path device uses an IR source coupled to a remotely sited receiver.
These devices can be used to measure ethylene along the perimeter or across a process area when installed at a defined spacing in one direction. In addition, open path detectors designed for use in ventilation ducting (short path length) can be placed in air intakes, including gas turbine enclosures.
For ethylene monitoring, open path detectors should be arranged in spacing spanning 1 m for areas of high congestion to 9 m for areas with low levels of congestion (3). The degree of confinement and obstruction is a significant factor in the propagation of a flame front and a fire or detonation’s hazard potential. At distances of 1 – 9 m, depending on level of congestion, overpressures resulting from flame speeds of 100 m/s will be than 150 mbar (2.2 psi), the threshold for major structural damage (4).
Typical alarm levels for point IR and catalytic detectors are 20 – 60% LEL while that for open path detectors is 0.6 LEL-m (20% LEL over 3 m for medium congestion).
When selecting a detector for monitoring ethylene, one must consider the potential for exposure to background gas, the operating temperature, and oxygen level in the atmosphere. Assuming the environment is reasonably devoid of other hydrocarbon gases, ethylene point detectors should do well for detecting unignited escapes of the gas.
Conclusion
As a key building block for the petroleum industry, ethylene is produced, stored, and transported in quantities that few other industrial products can match. To provide for its safe handling, chemical and petroleum companies must ensure the prevention of failure of pipeline and process and storage facilities which could lead to gas releases and fires and explosions. As the infrastructure to enable ethylene handling is deployed, ethane-based ethylene producers will invariably need detection techniques that are better suited to supervise the process fluid.
Several of these techniques are described in this paper. Infrared gas detection provides high integrity and reliability in point and open path configurations, essential for safety applications. Since optical gas detection is a physical technique, high target gas concentrations for prolonged periods and changes in oxygen level do not degrade sensor performance. Most importantly, IR devices are fail safe.
The acceptance for these techniques for ethylene monitoring is gathering momentum as organizations assess the type of gas release scenarios that might be present in the carbon capture and storage process. The techniques, however, are not a panacea and likely need more work in order to improve the performance of detection instruments, particularly over temperature extremes, for the most rigorous applications.
References
(1) Borchardt, J. 2007. Global Ethylene Supply Markets Shifting to New Geographies. Purchasing, http://www.purchasing.com/article/217183-Global_ethylene_supply_markets_shifting_to_new_geographies.php. Downloaded 1 July 2009.
(2) The Pipeline Safety Regulations. 1996. London, UK: The National Archives. Downloaded from http://www.legislation.gov.uk/uksi/1996/825/contents/made on August 12, 2013.
(3) Dorofeev, S.B. 2006. A Flame Speed Correlation for Unconfined Gaseous Explosions. Process Safety Progress26 (2): 140 -149.
(4) Dorofeev, S.B. 2007. Evaluation of Safety Distances Related to Unconfined Hydrogen Explosions. International Journal of Hydrogen Energy 32: 2118 – 2124.
Learn more about MicroWatt’s advanced Combustible Gas Detection solutions.
[DISPLAY_ULTIMATE_PLUS]
Ref: IPPT Industrial Process Products and Technology