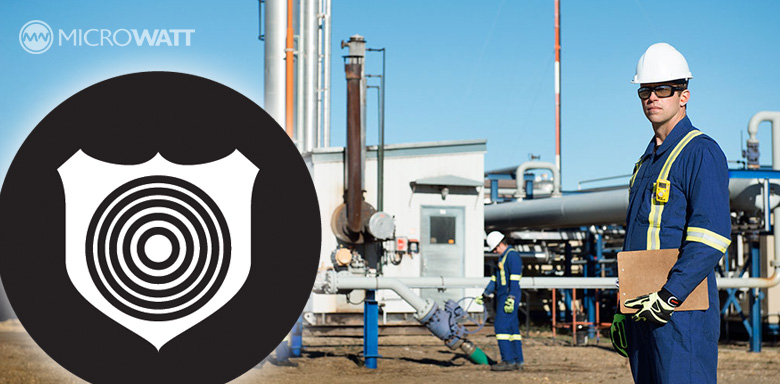
One of the greatest hazards affecting the health and safety of industrial workers is toxic, flammable and explosive gasses.
As Safety + Health magazine reported, concern over worker exposure to toxic and carcinogenic gases and vapors has increased in recent years. For one, the American Conference of Governmental Industrial Hygienists reduced its recommended safety threshold for exposure to common industrial gases including hydrogen sulfide, sulfur dioxide and nitrogen dioxide, all of which can be toxic. And the long-standing ISA 92.0.01 toxic gas detection standard, which has a strict performance requirement of a response in <30 seconds at high concentrations, will soon be lowered to increase the safety of industrial workers in Canada and the United States. All new products seeking the certification must meet the performance, or they will face a substantial product re-design. Meanwhile, many companies began voluntarily implementing zero-tolerance policies for low-level exposure to combustible gases previously considered acceptable.
More emphasis has also been placed on the long-term effects of industrial gas exposure. For example, the Canadian Cancer Society has found short-term exposure to gasses put off by the industrial chemical formaldehyde may cause headaches, watery eyes, nausea or skin irritation. While those symptoms alone facilitate the need for limited subjection to these gasses, an even bigger concern is that high or prolonged exposure to the chemical has been linked to cancer in some studies. The Occupational Safety and Health Administration has also tightened exposure limits on airborne concentrations of benzene in recent years due to its association with leukemia development.
However, simply increasing awareness of the risks of gas hazards isn’t enough to eliminate the problem. Gas detection methods, once as simple as the proverbial canary in the coal mine, have evolved to meet increasingly strict standards for worker safety.
Advances in gas detection technology
As the International Safety Equipment Association advised, modern gas detection systems should combine localized sensor detection with SIL certified fire and gas systems that have built-in redundancy, ready to provide automated mitigative measures such as visual or auditory alarms, deluge systems, or high-powered air exhausting systems. ISA has taken this approach even further by working with industry experts to develop ISA TR84.00.07, a true Lifecycle Engineering approach to Fire & Gas Detection system design.
According to Occupation Health & Safety magazine, advances in gas detection systems are also being driven by mobile apps and data collection.
Examples of this are mobile devices running apps which can be used to monitor environmental factors such as seismic activity or weather patterns that may compromise worker safety. In the event of a gas leak, networked smart sensors or personal monitors detecting elevated gas levels can transmit to wireless networks or directly to ruggedized, intrinsically safe smartphones running specialized applications, connected to the cloud. RFID tags, NFC tags, and Quick Response (QR) codes can be read by mobile device operating systems and used to aid in tasks ranging from automatic calibration to worker training. The mobile data made available is aiding worker safety by reducing human error and identifying gaps in safety procedures such as calibration or monitoring.
Additionally, wireless gas detection allows for real-time monitoring of gas levels. The units transmit environmental readings back to headquarters where they are monitored, allowing workers to be alerted to subtle changes in areas of their facility as well as serious threats. Wireless systems can even be programmed to automatically alert emergency response personnel in the event of certain pre-determined situations and notification systems can automatically direct plant personnel away from the danger based on the known precise location of the alarm.
Technology is also assisting in compliance with proposed new government regulations. For example, Canadian and United States regulatory groups are advocating for new regulations around mandatory benzene monitoring at petroleum refineries as part of an effort to reduce the risk of leukemia in surrounding communities.
The process would normally require manual sampling by personnel in order to monitor benzene levels both in the facility and at fence-line. However, wireless gas detection technology can provide continuous benzene monitoring that would not only comply with requirements but also increase protection for both workers and nearby communities.
Questions about how to effectively adopt these modern practices within your facility?
Contact the MicroWatt LifeCycle Safety Engineering group, we can help you to lower costs and optimize safety.
[DISPLAY_ULTIMATE_PLUS]
Ref: Safety Insights
Article Link: https://www.totalsafety.com