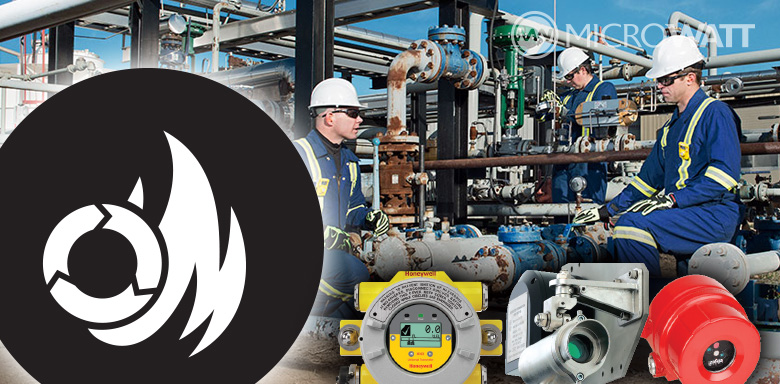
“How many detectors do I need?” and “Where should I locate them?” are two frequently asked questions about designing a gas monitoring system — and probably two of the most difficult to answer.
Unlike other safety devices such as smoke detectors, the location and quantity of gas detectors required in different applications has historically not been completely defined. However, technology and new industry best-practices can now deliver quantified safety coverage, operational efficiencies, and significant cost-savings when properly adopted.
At any industrial site, gas monitors utilizing various technologies have been traditionally installed throughout any area where hazardous gases are generated as part of an industrial process or a byproduct of it. Gas leaks typically appear around:
• Compressors
• Pressurized gas tanks
• Cylinders or pipelines
• Solenoid and relief valves
• Gauges, seals, flanges, T-joints, filling or draining connections
• Welded and quick-connect fittings and devices
• Runoff areas, confined spaces and loading/unloading areas
In addition, gas detectors are present wherever gas is stored or utilized for non-process functions. At an industrial site these locations can include boiler, furnace and mechanical rooms, chemical storage areas, maintenance rooms and more.
Installation Do’s and Don’ts
When designing a gas monitoring system, the following considerations should be kept in mind:
• Light Gases: To detect gases that are lighter than air (e.g., ammonia and methane), sensor heads should be mounted at a high level and preferably use a collecting cone.
• Heavy Gases: To detect heavier-than-air gases (e.g., butane and sulfur dioxide), sensor heads should be mounted at a low level.
• Air Movement: Natural or forced air currents can affect how an escaping gas behaves. Consider wind direction, runoff areas and confined spaces when spacing sensors. Mount the sensors in ventilation ducts if appropriate and always with the recommended adaptors. Utilize CFD [Computational Fluid Dynamics] adapted for gas dispersion mapping as part of your system design to ensure any escaping gas will travel to sensor locations quickly.
• Process Conditions: Gas movement can be affected by unique process dynamics. Butane and ammonia, for instance, normally are heavier than air, but the gas may rise rather than fall if it is released from a process line that is at an elevated temperature or under pressure.
• Environmental Conditions: The performance and consumption of the various gas sensing technologies can be negatively effected by temperature and humidity. This can create issues ranging from maintenance costs compounding unnecessarily to dangerous gaps in coverage occurring. Work with FGS experts to evaluate your application and optimize the sensor selection.
• System Architecture: More and more global operations are adopting the NORSOK design standard when it comes to their Fire & Gas Systems. This calls for a dedicated SIL2/3 rated Fire & Gas System for critical safety monitoring. This not only provides an extra layer of protection but it allows for continuous safety coverage no matter what the state of the process systems [monitoring during any temporary shutdowns or turnarounds].
• High-Pressure Systems: Sensors should generally be placed as close as possible to potential leak sources. However, with high-pressure systems it may be best to position the sensor further from high-pressure parts to allow gas clouds to form. Otherwise, there is potential for a high-speed jet of gas to pass by a sensor and not be detected.
• Accessibility: Sensors and their controllers/transmitters need to be accessible for functional testing, maintenance and servicing.
• Sensor Protection: Sensors should be installed according to the recommended orientation to ensure that dust or water will not collect on the sensor and performance is not compromised. A cover or shield can also be installed to protect the sensor in extreme applications.
• Unit Spacing: Too many detectors in a system has historically been the “safe” approach. Performance-based F&G system designs can deliver significant savings and optimize safety coverage.
Special Considerations
Gas Characteristics, Cloud Migration, Gaseous Mixes
Each gas has its own unique characteristics and exhibits its own behavioural tendency. Hydrogen sulfide, for example, is heavier than air and will sink; methane, on the other hand, is lighter than air and will rise. Carbon monoxide, carbon dioxide, ammonia and other industrial gases have a vapour density similar to oxygen, but can quickly displace oxygen when introduced in an enclosed room; asphyxiation or rapid gas poisoning is the threat here. The point is, each gas is different and must be evaluated accordingly.
Gas clouds can migrate into neighbouring residential areas and it is for this reason that perimeter monitoring strategies are used at landfills, wastewater treatment plants, gas refineries, chemical plants and other manufacturing plants; specific technologies such as open-path Infrared detection are used here.
Attention should be paid to interior rooms adjacent to a room being monitored. What industrial processes are performed or what equipment is used in these adjacent areas? Gases generated in those spaces can drift into other areas and cause a toxic/combustible mix. For example, a mechanical room that operates on flammable gases or a stockroom that generates carbon monoxide from forklifts can mix with off-gassing elements from hydrogen-charging stations, propellants used in heating elements and the like, elevating the risk of danger.
A common example is ammonia, which seldom leaks into an industrial environment as pure ammonia. Often, this type of leak contains vapours from other liquids such as lubricants and cleaning solvents. In one documented case, this changed the lower explosive threshold from 40,000 ppm (parts per million) to 37,000 ppm.
Conducting a Comprehensive Site Audit
A gas leak audit of the industrial environment should be conducted with gas detection experts on-site to determine the right gas sensing technology, strategic and economical siting of the instruments and the proper mix of fixed, wireless and/or area monitors. The placement of the gas detectors should be determined through collaboration among experts with specialized knowledge of gas dispersion, ventilation systems, process plant system and equipment, safety codes, and electrical requirements. Specialized tools and software will assist FGS engineers to quantify coverage as well as the level of safety achieved within the agreed upon coverage levels.
After the installation is complete, properly commissioning a system should bring the same parties together again. This process ensures that the gas monitoring system is fully functioning as designed and accurately detecting gas hazards.
LifeCycle Approach to Fire & Gas System Design
Work with a certified engineering organization that specializes in fire and gas detection system design (eg. APEGA in Alberta and APEGBC in British Columbia) who can provide services for clients ranging from conceptual development through to construction, commissioning, start-up and support operations – covering all phases of a Fire and Gas project lifecycle. Each solution is naturally tailored to meet the specific needs of the client. The goal is to develop a program for operators to move forward on their own with a safer operation based on preventative safeguarding solutions, rather than reactive – and ensuring mitigative measures are aligned with these designs. The two primary objectives are to complement traditional prescriptive Fire and Gas System design with modern, performance based practices that will quantify detection coverage, and to ensure that the effectiveness of the Fire and Gas System is maintained throughout its usable life by establishing a process for operators to effectively adapt to any future changes in the process environment being monitored.
Additional Knowledge Building
In addition to the above, leveraging training opportunities provided by either your gas instrumentation manufacturer-of-choice or the certified regional representatives is always good practice to improve your teams knowledge. Look for providers that employ expert instructors with a certificate-based instructional program on the use and routine maintenance of gas monitoring equipment. Instructors should be certified by the manufacturers they represent as well as having senior team members who are holding up-to-date safety designations from recognized third-parties like TUV Rheinland and exida (Certified Functional Safety Expert).
Questions about how to effectively adopt these modern practices within your facility?
Contact the MicroWatt LifeCycle Safety Engineering group, we can help you to lower costs and optimize safety.
[DISPLAY_ULTIMATE_PLUS]